5 Reasons Machine Tools with Hydrostatic Components Increase Precision and Decrease Costs
With hydrostatic components from Hyprostatik Schönfeld, machine tools achieve considerably greater precision, according to the company. This is made possible by the exceptional vibration damping and consistent true running. At the same time, the production costs are significantly reduced.
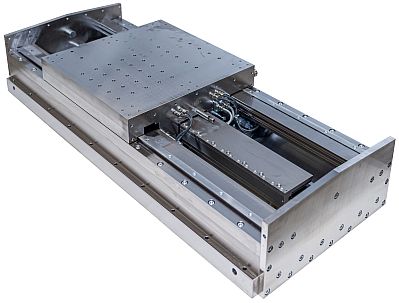
Hydrostatic slides are wear-free and consequently have an unlimited service life.
Five reasons for the difference:
- 1. No wear and tear -- Thanks to hydrostatic components such as lead screws and spindle bearings, machine tools display virtually no wear and tear. This results in high availability and low maintenance costs. Even with prolonged machine use, the high precision is fully retained.
- 2. Reliable true running -- Hydrostatic guides balance out short wave form tolerances of the guide surfaces, thereby achieving excellent true running.
- 3. No friction -- The friction of hydrostatic components is very low. There is no force surge when the direction of motion is reversed. Thus error-free circles can be moved with interpolation of 2 linear axis.
- 4. Exceptional vibration damping -- The excellent vibration damping enables a longer tool life, high surface quality and maximum cutting capacity.
- 5. Optimized oil flows -- The wear-free controller from Hyprostatik Schönfeld regulates the oil flows into the hydrostatic pockets, thereby achieving four times gap stiffness of what is obtained with traditional hydrostatic systems.
In addition, Hyprostatik Schönfeld works with specialized calculation programs in order to guarantee an optimum construction with respect to static and dynamic loads and permit optimum damping. By this Hyprostatic products can take max. load even up to max. speed.
Want more information? Click below.
Hyprostatik Schönfeld